3d-gedrucktes titan
Die additive Fertigung ermöglicht die Herstellung hochpräziser, langlebiger Bauteile – und schafft zugleich Raum für innovative Designs.
VOM PULVER ZUR PRaeZISION
DER TITANHEBEL
Der Hebel besteht aus Titan, einem Material, dass für seine außergewöhnliche Bruchfestigkeit und Korrosionsbeständigkeit bekannt ist. Titan kommt überall dort zum Einsatz, wo höchste Ansprüche gelten, etwa in der Medizintechnik oder der Luft- und Raumfahrt. Und das aus gutem Grund: Durch seine höhere spezifische Festigkeit im Vergleich zu Aluminium lässt sich mit weniger Material die gleiche mechanische Performance erreichen. Titan ist zwar nicht per se leichter als Aluminium, doch der 3D-Druck ermöglicht es einen Hebel zu designen, die gleichzeitig leichter und stabiler ist.
Im Inneren sorgen teils hohl gedruckte Strukturen dafür, dass das Gewicht weiter reduziert wird und gleichzeitig eine beeindruckende Stabilität erhalten bleibt. Titan reagiert weder auf Feuchtigkeit noch auf Schweiß, eine zusätzliche Beschichtung zum Schutz vor Korrosion ist deshalb nicht nötig.
Die Kontaktfläche des Hebels zeigt eine besondere Wabenstruktur, die mit klassischen Fertigungsmethoden nicht umsetzbar ist. Dieses Design spart nicht nur Material und damit Gewicht, sondern sorgt zusammen mit der speziell abgestimmten Oberflächentextur für ordentlich Grip – auch ohne Handschuhe.

DIE VORTEILE DER ADDITIVEN FERTIGUNG
Bei der additiven Fertigung wird feines Metallpulver Schicht für Schicht aufgetragen und mittels eines Lasers oder Elektronenstrahls selektiv geschmolzen, um die gewünschte Geometrie zu erzeugen. Der entscheidende Vorteil des Pulververfahrens ist die hohe Detailgenauigkeit und die Möglichkeit, komplexe, filigrane Strukturen zu realisieren, oder schwer zugängliche Geometrien wie Hohlräume oder interne Kanäle zu drucken – ganz ohne zusätzliche Werkzeuge oder Stützstrukturen.
Die additive Fertigung ermöglicht so, hochpräzise, langlebige Bauteile zu fertigen und innovative Designideen zu realisieren. Für uns ist es dabei besonders spannend, organische Formen zu gestalten – fließende, natürliche Designs, die mit klassischen Fertigungstechniken wie dem Fräsen nicht zu realisieren wären. Zudem lassen sich Wandstärken präzise auf die Belastungen des Bauteils abstimmen, was zu einer optimalen Stabilität bei gleichzeitig geringem Gewicht führt.
Ebenfalls hervorzuheben ist die Materialeffizienz. Nur das Pulver, das für den Druckprozess benötigt wird, wird geschmolzen, was Abfall minimiert und die Produktion effizienter macht. Überschüssiges Pulver kann nach dem Druckprozess erneut verwendet, und Stützstrukturen recycelt werden.
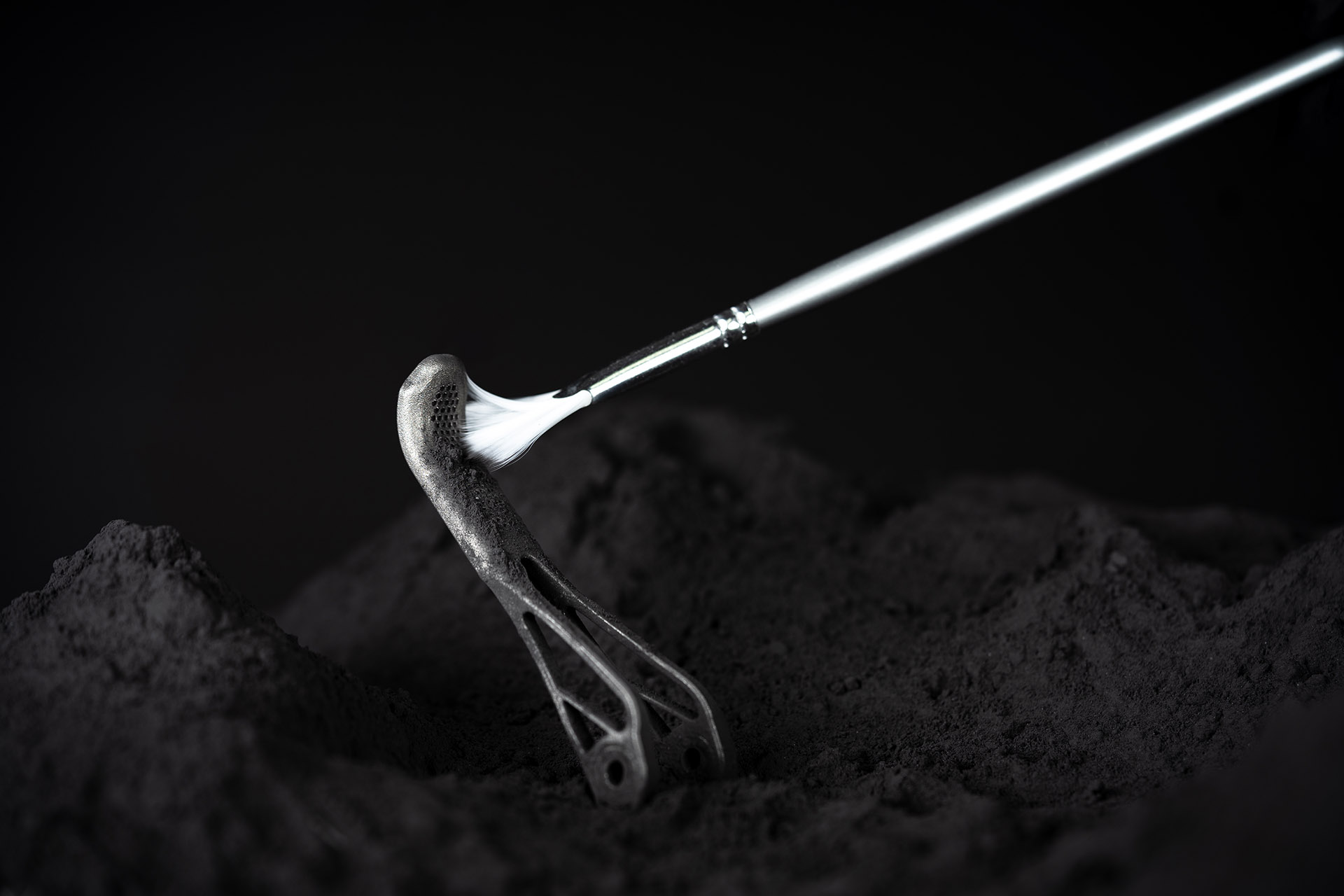
Die Geschichte dahinter
DER STARTSCHUSS
Die Vision war klar: Ein 3D-gedruckter Bremshebel aus Titan für unsere Piccola Pumpe.
Zusammen mit TRUMPF arbeiteten wir an neuen Designs und optimalen Fertigungsprozessen, um den ersten 3D-gedruckten Bremshebel zu entwickeln. Ein Jahr später konnten wir auf der Eurobike eine konzeptionelle Designstudie präsentieren und das Ergebnis vorstellen. Das positive Feedback aus der Branche hat uns beeindruckt und uns darin bestätigt, dass dieser Hebel nicht nur ein Prototyp bleiben sollte. Es war unser Ziel, das Potenzial der additiven Fertigung voll auszuschöpfen und den Bremshebel in Serie zu bringen.

VOM KONZEPT ZUR REALITaeT
Nach dem wir den 3D-gedruckten Bremshebel aus Titan auf der Eurobike präsentiert hatten, trat er in die nächste Entwicklungsphase ein. Aus den Kinderschuhen herausgewachsen standen wir nun auf eigenen Beinen, und es galt, neue Herausforderungen zu meistern: den Aufbau einer Produktionskette, die Weiterentwicklung und Perfektionierung unseres Prototypen sowie das Durchlaufen intensiver Testreihen, die den Hebel nach strengsten Vorgaben prüften – sowohl im Labor als auch auf dem Trail. Der Hebel wird in Deutschland gefertigt, was uns höchste Präzision und Qualität bei der Produktion ermöglicht. All diese Schritte führten dazu, dass der Hebel schließlich das wurde, was er heute ist.
